How to mount Cut to Backer Wood
Recently I acquired a box of cuts including CocaCola logo,
various Masonic items, MobilGas Flying Horse, Esso etc.
One of them is a Pontiac Indian Head logo which unfortunately has come off of it’s base.
I rough milled up a little piece of Red Oak to less than or equal to 3/4” thickness which seemed to be close to what all the others were for wood thickness. In all probability, I’m not going to try and print with this thing. Therefore following question is moot; would JB Weld work to bed the back of the cut to the oak? Just curious.
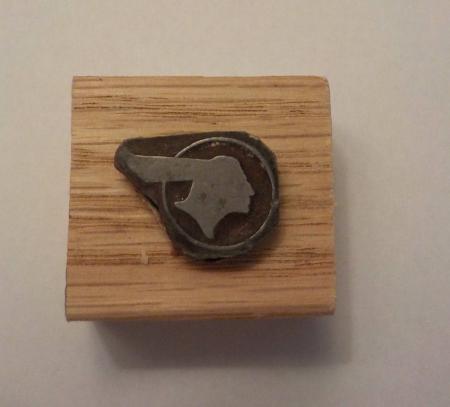
Pontiac 001.jpg
I use double sided carpet tape…the thin plastic kind. I also usually use 3/4” MDF to mount on.
I used to save un-routed blocks for 16-gauge plates that were in good shape for the 16-gauge plates that were in need of a new mount. Also saved blocks that were the right height for 11-point electros. Waste not, want not!
If the plate in question already had been mounted by cut nails, I nailed them (I still have a good supply of nails.)
Arie is quite correct on the double-sided tape; most cuts were mounted, in latter days, with a strong mounting cement, and were sometime nailed in critical places in addition.
You can guess that I’m from a time when nailed plates were still being made that way. Most photoengravers and electrotypers had at least one nailing machine.
Just Keep Printing!
Frank.
Arie and Frank
Thanks for input
Found another one that was loose/no mount
It has two nail/brad holes at diagonal corners and dimples on the back of the cut @ the nail locations. Are there specialized
brads for this purpose? Spiral grooved like flooring nails?
I will mic that cut on a piece of 3/4”. The dimples hold the cut off of the backing so some type of bedding or “packing” for cut seems indicated. Just brads used would be an invite
for wobble.
They’re just ordinary short brads.
If there are only two holes, I would use some double- sided tape AND the nails to make certain that the tape didn’t let go!
Also, smooth the dimples off the back of the cut with a file, so that it’s flat.
Just Keep Printing!
Frank.
Frank
I thought about filing the dimples down.
When I put a micrometer on this cut and wood
I cut to back it I came up significantly shy of.918.
Figured I would generously bed it JB Weld, let
it cure and then brad the thing. Here again, this
mounting of cut is for looks, not printing.
FWIW this cut is the American Amateur Print Association
or something close to that
Hey, reading small stuff backwards with my tri-focalled (sp?) eyes is getting to be an adventure.
Paste enough thicknesses of stock on the back of the block to raise it to .918. Use something tough, so that it won’t smash down, Pressboard is good for significant thickness difference.
Frank.
I would take Devcon Plastic Steel Epoxy over JB Weld for any application.
For nail-mounting, American Printing Equipment sold hardened brads imported from England, but for today’s relatively light use, any small brad should suffice, especially in existing holes.
With any tape mount, use a minimum of solvent.