Rollers shifting to the left
Hey Experts. I need some guidance. I have a C&P Pilot OS press. My new rubber rollers with new trucks from NA Graphics are shifting to the left with each pull of the press lever. Eventually, they will fall off or the right saddle will lock against the right roller arm. I have tried the old rollers which have adjustable trucks and they do not appear to move around very much. Could this be a spring tension issue? Maybe the left spring is tighter than the right spring? There left spring is 1/8” shorter (more compressed) than the right spring. Any suggestions or other ideas?
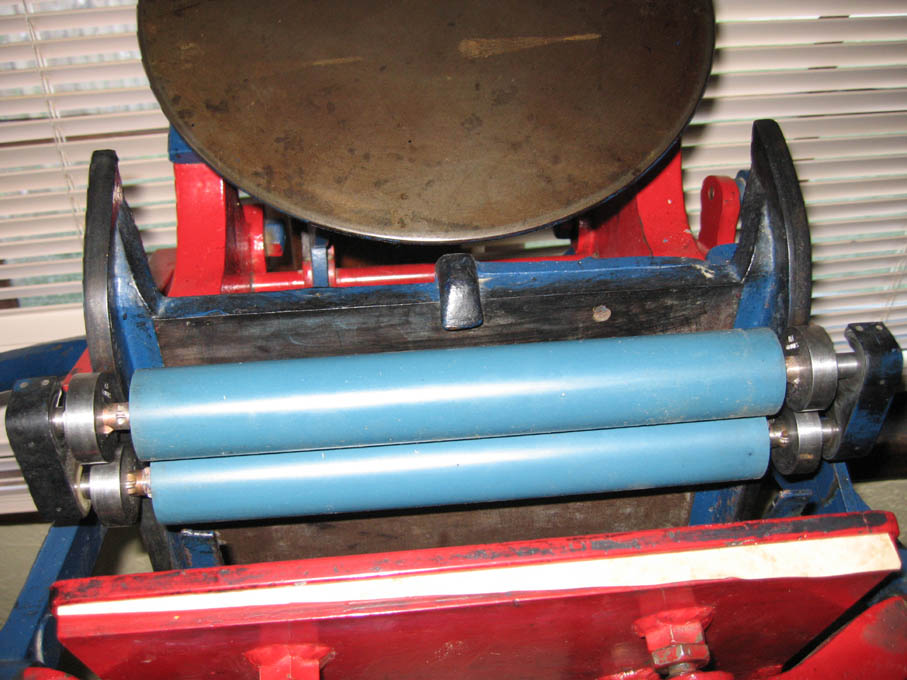
One solution is to put washers between the press saddles and the trucks so the shaft of the roller cannot run one way or the other as far. You just need to make certain the trucks don’t drop off the runners on the sides of the press bed. If you go to a larger hardware or home center, they may have bronze washers which are of greater thickness than the common steel ones. Just make certain the hole in the middle is large enough to fit the cores, but not so large to be sloppy or the operation will be pretty noisy when printing.
If the trucks and rollers are new, they should be keyed to each other so the trucks stay in the correct position and do not move in toward the rubber roll cover. The washers on the outside of the trucks will just keep the whole assembly centered and on the tracks. Ideally, the trucks should be wide enough to do the job by themselves, but apparently this is not the case with yours.
Amy -
Try reversing the rollers and see if the shift moves in the opposite direction. This is a strange phenomenon and will likely have a unique solution. Make sure that the inner surface of the saddles are clean and smooth.
Check to make sure that all of the nuts and bolts on the side arms are tight.
Try using your old trucks on the new rollers and your new trucks on the old rollers and see what happens.
Spring tension should not be an issue, and if your old rollers don’t exhibit this behavior, it is likely something different with the new ones. (duh.)
I don’t think that washers are the answer, and binding agains the saddles is something to watch out for. But I’ll bet if you give Fritz a call at NA Graph, he’ll be ready willing and able to assist you in solving the problem.
Let us know what you find out.
-Alan
jhenry, the new rollers/trucks are keyed to each other. I did have to file the nibs down to fit the trucks properly. I wonder if I find washers if there isn’t a rubber washer to place on the outside edges to protect the saddles.
Alan, I’ve tried reversing the rollers and same shifting happens. I can’t get the trucks off my old rollers (they are corroded on) or that would be my next step. Although, they are very worn and much smaller in diameter than my new rollers. I would then have many layers of tape on my rails to get type high inking. They are however, adjustable trucks and are much wider and softer than the steel trucks. The steel trucks are about the same width as the rails.
Do you think that I might have the wrong trucks for my press?
Amy -
Your trucks are probably the right ones. I just installed new rollers on a Pilot and also had to file down the nibs to fit the trucks on them. I don’t think that is the problem.
see: http://excelsiorpress.org/photos/rollerends.jpg
and
http://excelsiorpress.org/photos/rollertrucks.jpg
If you look inside the trucks, you’ll see that the keyways are sloped. As you file down the nibs (slightly!), the trucks will fit in closer to the rubber. I also filed down the other two nibs that are closest to the rubber. Those I filed carefully from the side so that the trucks would press against them.
This is how I discovered that the trucks had to be in closer to the rubber. Until I did, they were binding on the saddles, did not line up properly on the tracks and the ink rollers were sliding, rather than rolling over the form. That truck-to-saddle clearance is critical.
If you reversed the rollers and the same shifting occurred, the problem is likely in the arms, not the rollers or trucks.
Does the ink table rotate freely?
But here’s a thought. When you changed the rollers, did you perhaps also rotate the saddles? Although they seem to work either way, there is a minimal difference in the alignment. It might be worth a minute to check that.
Otherwise, sorry to say, now I am at a loss for suggestions…
I’ll study the action on my New Style Pilot and see if I can think of anything that might cause what you’re experiencing.
————————————————————————————-
But - for what it’s worth, you can remove the old trucks from the old rollers. Oil them well with WD-40 or some other special light anti-rust oil first. Then get an open-end wrench that fits over the shaft, but not the trucks.
Better yet, if you have acess to a tie-rod end fork (for changing tie rod ends on a car), it’s a simple task to support the wrench (or, better yet, the fork) and hammer the roller shafts through the supported trucks. I used the edge of my Vandercook, but a vise - or any steel table with a sharp edge - would be a good place to do this.
You can also try soaking the roller ends in either Muriatic acid (from pool supplies at Home Depot) or that interesting concoction of vinegar & lemon juice - which I have not tried yet. Either should help remove the rust that’s locking the old trucks to the old roller shafts. Then hit it with the oil and try the tie-rod-end-fork trick.
If I can think of anything else, I’ll be back and post it here.
- Alan
It should be physically impossible for the rollers to fall out of the roller saddles. The roller core should be 14 1/4 inches long and the outside of the bearing surface of the truck should be 1 inch from the end of the roller core.
Amy -
Ref John’s reply: The only thing I can think of that would make the rollers come out of the saddles were if they were to actually roll out of the saddles due to an overly tight fit between the roller shafts and the saddles or an absolute lack of spring tension to hold them in. You did mention some doubt about the spring tension..
If the saddles were rusty or the shaft fit were too tight (so that the rollers did not move freely in them), they could work their way up and out of the saddles. I have seen this happen on table top presses. Is this a possibility in your case?
- Alan
I went back to my original posting and added a photo of my rollers on my press. This is a picture I took before I filed my core nibs. The trucks now fit a mm or two closer to the rollers and more aligned with the rails.
John, the trucks are falling off the tracks which causes the top roller to pop out of the saddle. It happens mid pull. Cores are 14 1/4 inches.
I don’t think my springs are too tight since I can pull my saddles out to fit my rollers. My saddles have some play. I can twist them slightly side to side. Is this ok?
I went to the hardware store last night and bought an assortment of washers (3/8 inch core) and a few neoprene washers to put near the saddles. I can try this out tonight and see if it helps.
Updated. Amy -
Interesting photo. But it appears from the photo that your rollers may be larger in diameter than your trucks - or is that just a trick of the camera?
Another thing - are those rollers touching each other!?? If they do touch, that would most certainly make them jump out of the saddles…
- Alan
I have the German version of the Pilot so I am going to assume the C & P is nearly the same. I think your problem might have been caused by the previous owner who used the adjustable trucks. I wanted to use adjustable trucks on mine and they were too wide so I had to reverse the saddles. This is done by driving the pivot pin out of the saddle. The slot in the back of the saddle is not in the center so reversing them increases the distance from inside to inside. If this is the case with yours, which from the picture surely looks like it is, you’ll need to remove the springs and saddle / slide rod and drive the pivot pins out and put the saddles back there way they were originally. You might have to peen the end of the pins to fatten them a little before you put them back to make them snug or a little JB Weld epoxy will hole them tight too. You definitely should not have the space between the trucks and saddle that shows in your photo.
Musikwerke -
Interesing idea, but when I tried rotating the right side saddle on my New Series Pilot (there was a pin on the left, but not on the right), I found that the saddle hit up against the side arms of the press and intefered with the action.
Thanks to all of you for your help and advice on my issues. The technical support has been amazing. I am so lucky to have found the Briar Press community.
Musikwerke, Very interesting. I have an unworking Pilot NS press in addition to my OS and I looked at the saddles on it for comparison. They do look like they are positioned closer to the trucks.
Today I tried out the washers that I bought the other night. Guess what? They worked beautifully. No shifting to the left whatsoever.
So, now I’m on to my next problem of taping the rails. My new rollers inked my Boxcar base. Now, I go through the trial and error of finding the proper amount of tape to position my rollers type high. I’m off to find the thread about that…
The pivot pin, the one that secures the saddle to the slide rod has to be removed if you want to rotate the saddle.
Amy,
If you are going to leave the saddles the way they are, why don’t you get a new set of adjustable trucks? It appears, from what you said, that you need to raise the rollers anyway and the expandable trucks are just the thing for doing this. Once they are set you should be able to forget about that adjustment, especially on a hand press.
Morgan Expansion Trucks are no longer made according to Fritz at NA Graphics.
Amy:
I’m glad the washers worked for you. I have done this in the past with a different press and found it to be a very good means of keeping the rollers from running off the rails. I don’t suggest a solution unless I have used it myself. No need ot confuse the issue with suppositions.
I used a bronze washer, so there was no problem at all with wear on the saddles. The neoprene washers might wear a bit after time, and you could probably find a couple bronze ones or nylon which would be tougher and yet would not wear on the saddles.
Solve one problem at a time, and you’ll keep your sanity. The roller height issue has many solutions, and taping the rails is a good one to one to begin with. There are some industrial tapes which are made of polyester, which has no “give” to it. An example is 3M #850 tape. Each layer is jsut under .002”, so you can build it up to whatever you need and it stays fairly uniform. I use this on my old Kelsey Union press (c. 1890s) to adjust for seasonal changes in the composition rollers I sometimes use. I have a set of rubber rollers which I have no problems keeping at correct height.
John Henry
Washers will provide a ‘Farmer’s Fix’ and will probably do just fine. However, that approach does not address the initial problem of uneven tracking. Here’s a suggestion;
The problem was not there prior to the introduction of new rollers and trucks, as I understand you. Therin lies the starting point. Now, while the rollers could cause a pulling from center, I rather doubt it because in order to have that effect they would probably be noticably out-of-round or tapered. Thus, an examination of the trucks and rails is in order. Short of determining truck trueness by use of a micrometer or dial guage, try this: Clean all ink from the rollers and ink table. Coat the trucks with Prussian Blue, fit them to the rollers, mount as centered, then slowly move them through their entire range from bottom position to ink table. Rest them (momentarily) on the table and examine the pattern left by the blueing on both trucks and rails. I believe that pattern will tell you where the problem lies. To my mind, the rails are not providing a stable track for the trucks; or, conversely, of truck to rail. Either there is rail wear - not noticeable with rubber-tired truck, or the crown on the truck is such to cause wander (think flat belt/pulley drive). Taping the rails, (providing a cushioned track) might well provide some relief. But that, too, is but a stop-gap measure often leading to other temporary fixes. Did you ever use your old trucks with the new rollers? That might also solve your problem. Just some thoughts. And my opinion.
Laurence
Actually I had exactly the same issue on my NS Pilot, with brand new rollers and trucks from NA Graphics. Basically there was about 8mm space between the outside of each truck and the saddle, so after a few pulls the roller would shift enough to make the truck fall off the track. This was easily solved by a few washers on the outside of each truck as other people have mentioned, which served me quite well for many jobs.
Its hard to believe that the rollers and trucks will stay perfectly centered on the tracks if there is nothing to keep them there, like the action of them bumping into the saddle on one side or the other. I have no explanation of why my new set of rollers and trucks apparently was not the right size for the press I bought them for, but maybe I’m missing something.
For my new press I had to machine trucks and roller cores from scratch and I just size the delrin stock I used to make the trucks to be the right size to keep the roller/truck combo riding on the rails between the saddles with a few mm of running space so they won’t bind against the saddles.
Hate to repeat myself but here goes. I wanted to use adjustable trucks on my pilot press. The only way this can be done is by REVERSING the saddles. Cowan adjustable trucks are at least half again as wide as standard trucks. On both roller arms I had to unhitch the spring and slide the rods out of the arms. Then I used an arbor press to push the hinge pin out of the saddle. Once that is done, the saddle can be rotated 180 degrees and reinstalled on the slide rod. Doing this to both sides increases the inside to inside distance of the saddles so that the adjustable trucks will just fit. I wouldn’t be a bit surprised that leaving the saddle in this position and going back to standard width trucks would cause the rollers to move all over the place. Washers are the lazy person’s fix. And the down side to not putting the saddles back to their original position is, the roller core is not riding on the full width of the saddle and over time, both will wear prematurely and unevenly and you may wind up with roller tracking problems that you can never rectify. I abandoned the adjustable truck idea on my pilot press for this reason alone.
Well, now I’m wondering if I should take my washers off. I don’t want to injure my press further. I have switched inks and found that the smoother, less tacky the ink, the less the rollers shift. So, maybe I’m good now without the washers. I’ll give her a go. One thing I’m learning about letterpress is that there is a continuous tinkering (at least for this novice) and it makes for a more intimate connection to the final printed piece.
Amy,
Regardless of if you have the washers installed or not, center the rollers so that the trucks are lined up on the rails. Next, check to see if the ends of the roller cores are flush with the outside edges of the saddles ( or slightly protruding). If they are, then the problem with the excessive space is due to the roller manufacture and using washers to take up the slack is a good and safe remedy. However, IF the ends of the cores are landing (riding) somewhere in the center of the saddle, I feel certain that the previous owner of your press did the same thing I did and reversed the saddles to increse the width so that adjustable trucks could be installed. A person who is reasonably handy with simple hand tools should be able to flip the saddles end for end. By ‘flip’ I mean removing the saddle hinge pin, turning the saddle 180 degrees and reinstalling it on the same arm. The worst that can happen is it makes matters worse and you can always put them back the way they were.
I’ve had this same problem with a Craftsmen Superior. I tried the washers and they sort of worked, but were very noisy. I also tried a metal flat bar expoxied to the outside of the saddles. This worked better, though sometimes the epoxy lets go and the bar has to be re-glued.
Now, my press is probably seventy or more years old and I have no idea what parts may have been swapped out over the decades. What I have noticed is that after I clean the press, if I am not careful to put the trucks back on the shafts EXACTLY as they came off (same truck to the same end(s) of the same shaft, and turned the correct way, the problem recurs.
That the truck keys are supposed to be tapered is something I did not know and perhaps that will prove to be an essential clue. It seems to me that this design without some method of keeping the truck from sliding on the shaft would be rather like taking the rims off of the wheels of a freight train. The train might possibly stay on the tracks for ten or fifteen feet, but then the wheels would slip left or right and the train would de-rail.
Looking at my press and considering how complex it has to be, I guess it is amazing that it works at all, never mind working well. If I ever move my print shop from the former dining room and into a larger space with a concrete floor, maybe I’ll get a larger press and can discover some REAL difficulties.