C&P Fade
Hello,
I’ve been trying to trouble shoot this issue and am looking for any suggestions. Using a C&P 10 x 15 press. When printing, there is an obvious “fade” in our prints from bottom up. Wondering if anyone has dealt with similar issues. I’ve tried adjusting the rollers (I have Morgan expansion trucks). Wondering if this is the platen being unleveled? Have been using polymer plates and it has happened on multiple plates. See attached for image. Since using this press I’ve never messed with adjusting the platen—seems intimidating and don’t even know what tools to use for that. Thanks for any helpful insight anyone can provide!
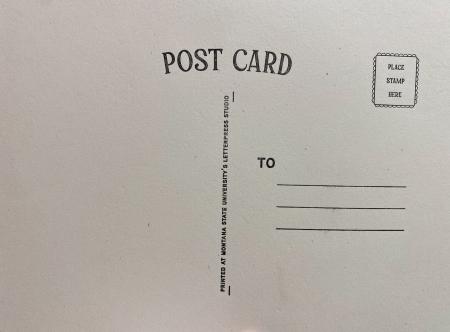
Fade.jpg
If you rotate your plate 90º does it still happen? To me it looks like an over inking issue and maybe a problem with rail wear or form flatness. This doesn’t look like a platen leveling issue unless you’re noticing more impression on that bottom part. If that’s the case then you’d be able to adjust your makeready before going all in on a platen adjustment.
Bradley.
Morgans and photopolymer are not the best combination. Morgans need regular replacement of the tires to maintain concentricity, and if you also over-expand to compensate for low roller tracks, eccentricity is very likely.
Eccentric rollers will give uneven inking in their direction of travel, and flaws would shift up and down.
I knew one printer who took a set of the Morgan trucks and had nylon tires machined to fit them to roller diameter.
Hi, this is a problem of elimination of variables. First use a roller gauge to check the dimensions of rails. Are they the same dimension?
You may have to rig a jig and grind them to a set distance all the way along the rail on both sides so they are the same, whatever it is. Every press had a set distance for the rails, whether type-high or something other. You may on occasion just shim them up to type-high. Expansion trucks are a cheap and dirty way to do this same thing. Rubber expands and contacts with time and toil.
A jig can be something as simple as two pieces of mild 1/8 inch steel flat stock 3 or 4 inches wide, cut to the length of the bed, fastened in place with robust C-clamps so they are parallel ‘with the bed’ so you can grind the high spots out to give yourself a flat surface. A file, a die-grinder even a good belt sander will work. This is not difficult nor hard to rig. Some more elaborate platens like the high-class C & P 12 x 18 presses had adjustable roller ribs to eliminate this problem. Early cylinder presses had adjustable roller guides for reasons that will be evident. But regardless all roller ribs/guides will wear with time especially if the trucks used were made of relatively hard steel against the cast iron roller guides.
Next, get some solid trucks for the rollers, and check whether the cores are straight. Nylon trucks are the best thing since they do not wear the rails out over time. Use Nylon that is very hard like Delron, rather than soft. Even solid trucks of the past are OK, although if they are not round then this introduces another variable. Every press with solid rollers had a set amount of ‘roller squeeze’ governed by the roller and truck diameter. Generally for a slow speed press I found that three to five thousands of an inch sufficed when the roller ribs/guides were set at whatever you know is type-high. Others may disagree about the amount of roller squeeze but it is itself governed by the diameter of the rollers.
Most problems of inking are not necessarily a consequence of roller squeeze. If there is roller wipe it is likely that the roller pressure is too extreme; perhaps the roller carriage is warped or bent or impeded; in additon, are the roller journals round and properly supported?
When people used composition style rollers, that expand and contract in the weather, adjusting roller height with a gauge (one with a long handle at type-high, whatever that figure is in your country) was common. Rubber stays pretty stable for a long time until UV and roller washes degrade its surface.
So unless you verify bed rail height, roller dimensions (parallelism and round-ness), have a certain truck diameter, then inking problems will persist whether one uses lead composition or photo-converted composition. The same process works for cylinder presses, automatic feed platen presses, table top presses for single lines of type, or Compound or Universal hand-fed platen presses.
Of course the last-most variable is the roller itself: is it ground properly and is it the same diameter along its length? Is the rubber the right durometer (hardness) for your press, for the inks you use, for the temperature of your pressroom, for the speed at which the press operates?
Nearly all the machinery used in relief printing is well past the date of use envisioned by their makers, so radical repairs such as grinding the roller rib are not outlandish. One can glue shim stock on them, or have a machinist prepare a shim, drill small holes and thread them for a bevel headed screw so you can take them off to shim underneath in the future. Such repairs are simple for a machinist but may be expensive.
On the other hand, restoring a press to function is not just a question of paint and polish. One may need to have new trucks and journals made or roller cores. Unless you eliminate these easy variables the more difficult ones such as impression, makeready (on bed or in platen), ink composition, forme imposition will be harder to regulate.