C&P 8x12 small head and lock cam fitting to main shaft
I’m getting ready to put my press back together and I foresee a problem fitting the small head and lock cam to the main shaft already attached to the large gear cam wheel.
Can I please get some tips/ DIY solutions. When I originally removed the small part it took a 12ton hydraulic 3-leg gear puller and some hacking. If there aren’t any reasonable home/DIY solutions, what’s my best option?
Thanks in advance.
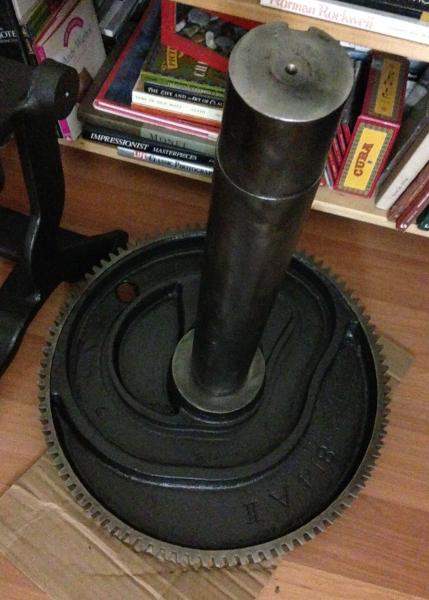
Large gear cam wheel and main shaft
Didn’t attach the second image
Small head and lock cam
Looks like fun, forgot all about this one, last time was about 35 years ago. The only thing I can tell you is make sure all surfaces male and female are clean and debured, use a fine emory cloth on both. have a fresh keyway, oil all parts and slide carefully together, yeah I know, on my 8x and 14x we used some pipeclamps (wood working) to apply pressure and a heavy wooden block to beat it back into place it will go back easier than it came off. Good luck, hope this helps.
Ditto on the above comment re: clean, smooth surfaces.. Lots of grease, a few helpful hands and a rubber mallet.
Not foolproof, but works well 90% of the time.
With just a 1/16” (of an inch) leading edge filed onto the the very end of the shaft, (to give the hub a fighting chance of entering initially,) and then play a D.I.Y blowtorch into the actual hole in the Hub, (upright so that the heat goes all the way through) as opposed to down hand.
Probably less than 2 minutes.!!
The principle:- to expand the hub by a fraction.
This system *borrowed* from our Auto engineers a long, long, time ago when the only recognized method for fitting Auto Starter Rings was as above, i.e. by playing Oxy/Acetelene heat onto the new ring and dropping it onto the Flywheel.
Even if it (the ring) did not make it home on the initial effort, it was a doddle to bring it down to register with a Copper or Brass drift, as implied above,! but variation, I.E. assisted with 2-4 Lb. Engineers style Hammer and Copper/Brass plate across the flange of the hub to protect.
One extra gimmick, still possible Maybe! (way back) would have been:- Printers lead from the Ludlow, Lino, Elrod, Monotype, poured into a (DRY) Bean Tin, made and still makes the best >>Bar None<< combined, Drift, Hammer, etc.
You must surely have, not too far away, Fishermen, who cast their own weights andor Re-enactment Guys who also cast their own Bullets, IF there is no Hot Metal type caster`s handy.
Thanks a lot for the feedback, I really appreciate it. If anyone else can pitch in, please feel free to do so.
to reverse press the cam back on my kluge I drilled and tapped a 1/2 in hole in the end of shaft threaded in a half inch length of grade 8 threaded rod placed a large piece of steel drilled out with 5/8 hole in center press that flat to your cam and use grade 8 nut tighten till cam slips back on if you have porta power tools you can jack that sucker back on in a flash
these are tools used to replace head cam, that is, if it doesn’t slide right on. a lot of these old machines had a loose fit here.
1) make sure oil is indeed draining into main shaft bushing.
2) make sure oil is draining into the rocker roller.
3) install main shaft and rocker roller. turn to insure free movement for full rotation. pay careful attention to the roller in that it is not binding at all.
4) once you are ready to install the head cam, use “C” clamp to lock the main shaft in place with the keyway “up”. clamp the main gear to the frame so it cannot move out or turn.
4) clean the head cam of all grease and oil possible. put it on the heat plate, turned on high. a piece of sheet metal can be used to cover the main shaft hole on top, with an over-sized box covering the whole thing. let heat for about 45 minutes.
5) some grease smeared onto the protruding main shaft helps with install.
6) remove heated head cam from hot box and install onto protruding shaft. the heat will give you about 5 seconds to align the 2 key ways. do this quickly.
7) Line up key ways and insert/ tap in key, some pre fitting on the key and ways to make sure the key will slide in to the void helps. the key should slide into the head cam and shft slots snugly, but without galling.
8) give the hot cam 60 seconds to shrink, then release C clamp and turn over, feeling for any major tight spots. minor ones are okay and will be adjusted once cool.
9) once cooled to room temp, turn the shaft over feeling tight spots. tapping the end of the shaft in those spots should relieve it. if there is side to side play, then tapping on the head cam itself to tighten the fit. hit the cam as close to the shaft center as possible. Tapping can progress to Hitting with a heavy sledge. reclamp the gear in this case
head cam tools.jpg
ericm, Thank you very much for the information you provided. Your trick worked like a charm. Thank you again ;)
Nice! Glad it worked. i have done this many, many times. With bigger 14x22 head cams there is a lot of really hot, heavy, metal involved.