Paper Order Update - Bad Cutting Job!
My order of Somerset paper and this is how it arrived. An entire parent sheet’s worth…
I can’t get them on the phone today so I’ll give it until “after” I speak to them Monday until I blurb out their name in anger!
Second time they have done this to my orders.
Has this happened to you? I know I need my own cutter!!!
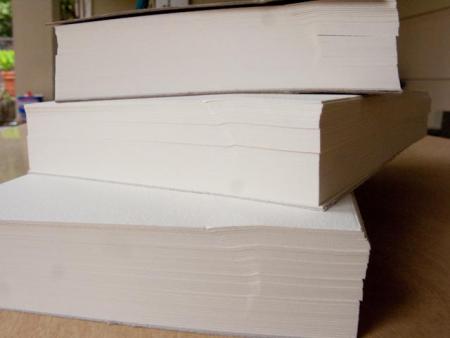
IMG_0976.jpg
Ouch…what did the shipping carton/packaging look like? Was it damaged? If so, you should reject it when it is delivered.
I’m looking at your pictures, and I see stacks of paper out of the packet. Your comments and pictures don’t tell the viewer:- Was the paper properly wrapped in industrial standard wrapping paper for moisture control and safe delivery? Are the sheets cut out of square? Are the sheets all variable sizes? Are the sheets mixed grain? Are the sheets all of the same grammage? Are there any blade marks on the side of the stacks?Is your supplier a recognised paper merchant? What does your Official Order ask the supplier to do? What was the time frame for delivery? What is your credit rating with the supplier? Your comment “an entire parent sheet’s worth” indicates that you are new to this aspect of the trade. Having spent many decades working for, buying for and buying from paper merchants I can say this aspect of the trade is the one that will send a printer broke for many reasons and not necessarily caused by the paper merchant. Consider enrolling for my “Print for Profit: Costing, Estimating and Quoting” course. I would seriously advise against naming and shaming on this website until all legal steps are taken in the land where you live and then probably, never!
William Amer, historic Rockley NSW
girl- The box was fine. That damage was done when it was cut. Second time it has happened.
william- no x 10 (+/-)
In my experience this kind of damage is caused by cutting on the wrong side of the cutter with a less than sharp blade. If the paper is cut on the left side (the blade on most cutters comes down from right to left) the blade tends to push the cut-off stack against the frame and buckle the paper, causing this kind of damage. Soaping or waxing the blade can lessen this tendency. The face of the blade must be clean and preferably polished. I prefer to cut on the right so the cut-off stack has room to move, but some cutters have the paper guide to square against on the left.
Bob
I don’t believe secondbob was naming/shaming anyone. That is a BAD cutting job and should be rejected IMHO.
William Amer,
Why be so obtuse? Secondbob was merely asking “Has this happened to you?”
There was no need to launch into an impersonal rant / sales promotion exercise for your own personal profit. If you bothered looking into secondbob’s account, s/he is based in the USA, and highly UNLIKELY to fly to remote Australia to enrol in your “Profit: Costing, Estimating and Quoting” course.
Suggesting that a credit rating with a supplier will particularly determine how the merchant cuts the paper is laughable. What’s more, suggesting that your profit estimating course, held in a different country, will solve this problem is arrogantly inappropriate,bordering on deceit.
The only naming and shaming that needs to be done, is your particular post. As a community, we need to focus on getting off our high horse, and adapting to conventional norms of the internet in 2011. ie: Leave the ego at the keyboard, and be a friendly, welcoming and helpful community.
Let us know how you go secondbob.
Looks to me like the stock was mangled before it was cut.
I’ve had stacks look like this after cutting stock that had an edge bent in shipping.
I’ll let you all know what happens when I call them Monday.
I KNOW you all have used this company before…
Have a good weekend everyone!
-sb
Oh no - that is dreadful! I recently had a box of envelopes arrive which appeared as if they had received water damage and the packaging ink had bleed off onto the envelopes. The company was very apologetic and has replacement envelopes on there way to us. Fingers crossed that you get such a speedy service to fix this pretty apparent bad cutting service.
jeez Will… they still have soap boxes by you?
I’ve had some “bad paper” experiences, but this case is just ridiculous.
Surely the person packing up the sheet for shipment would notice such damage. Perhaps they just did not care.
Secondbob, I would like to know the outcome of this story.
Sommerset is a fragile paper, easily damaged, we use it a lot. Never cut it on a power guillotine in large stacks, the paper is bulky and compresses easily. We cut in small stacks with low clamp pressure and a sharp knife or on a Boardcutter. If you have a commercial paper house cut your paper, you have to alert them to the Fact that it is a mould made paper and damages easily. The Sales Guy you talk to may have knowledge in paper, the guys in the back office, who pack and cut - they don’t. They do a job they get paid for.
I’ve bought all my paper from local Paper Factory Merchants, where you don’t have to have the paper shipped. (Cash and Carry) If it was shipped speciality paper it was always double boxed. Most of my paper comes on pallets in full sheets, & wrapped in plastic.
There are safe guards they can use to cut this type of paper. I have several for my 31” cutter.
Update:
I told them the story and they are re-cutting the order at another facility (NJ) not the original shipping warehouse.
They are send me a RA and I’m to mail the order back to be used as samples.The owner got on the phone with me and was great.
Other than being delayed a week…not that bad of an experience with this company.
-sb
Having spent Easter and ANZAC Day away from my computer, I return and see that I have overstepped the mark nwith an earlier comment. I wish to apologise for any offence given, to the original correspondent, the good people of Briar Press and those that know me personally. My only defence is my zeal and enthusiasm for Letterpress, which on this occasion was misplaced.
William Amer, Rockley NSW
No worries William…It’s good to read posts like that every now and then…keeps us all on our toes!
take care
-sb
William, I wish you’d teach a course like that here in the US. I could seriously use some help in that area…
William, most of us are printers, you’ll have to do better than that to offend us. Dick G. ps love reading your posts.
It looks like the company that cut the paper do not take care of their equipment. The blade is damaged. I small nick in the blade will cause this problem.
Blades should be sharpen on a regular basic, and many companies that have poor operations, would rather ship poor products than do the job right.
All it takes it a staple or an small metal object to be cut with the paper cutter and the blade will be damaged.
This work was done by a poorly trained employee.