Dauchy & Co. Compositors’ Rule, 1869–c1930
Sometime between 1869 and c1930, rules like this were presented as gifts or sold to clients of Dauchy & Co., a prosperous advertising agency in the New York financial district.
It measures only agates and nonpareils, type sizes used by compositors employed primarily by newspaper publishers. This super-rare instrument is apparently crafted from ivory and German silver.
The “incestuously inbred” history of Dauchy & Co. is v-e-r-y interesting! Besides the fact that, possibly single-handedly, it nearly destroyed the entire US metal type industry, it spans juicy stories connecting William H. Page with Henry Brehmer and Jell-O and again poses the brain-boggling puzzles, “Who exactly was Robert Lindsay?” and “Who exactly was Robert A. Lindsay?”
Please take a peek at the webpage illustrating views of all six surfaces of this artifact and my research of it:
http://bazaar.typeheritage.com/dauchy/
If it interests you, please respond to the forum topic about it: http://forums.typeheritage.com/topic/dauchy-rule/
As always, my preferred documentation sources are 19th-century professional journals, producer catalogs and design patents.
Many thanks for your feedback, Anna
Author, The Type Heritage Project
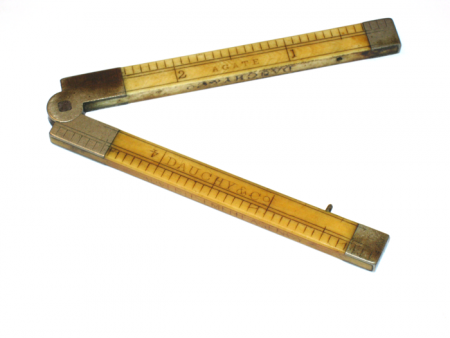
01-Agate.png
With apologies… I posted the message about the Dauchy rule:
http://bazaar.typeheritage.com/dauchy/
before publishing my own forum topic!
Duh, it’s fixed now:
http://forums.typeheritage.com/topic/dauchy-rule
Thanks again for your kind feedback,
Anna
I am intrigued by your bold claim that Dauchy ‘nearly single-handedly destroyed the entire US metal type industry’.
In over forty years of studying type and letterpress printing I can honestly say I don’t think I have ever even heard of them!!!!!
Can you direct us to where we can learn more about this?
Thanks
Rick
Dauchy was closely allied with the Lindsay Type Foundry, notorious for electrotyping competitors’ designs.
I learned quite a lot about them in my research of this artifact and reported it here:
http://bazaar.typeheritage.com/dauchy/
You’re welcome, Anna
I too had not heard of Lindsay or Dauchy in my research, primarily in the Inland Printer. I am making a note to seek these names out in my readings from my collection of IP’s that begins with the 1886 bound volume. I am currently reading the Volume 20 of the IP that covers 1897-1898 and the predominate theme was the influx of “machines” into type setting. The December 1898 issue is particularly interesting, covering a number of fascinating subjects but also including a new column titled “Machine Notes and Queries” that covered linotypes and other mechanized type setting machines. The linotype was in use in most of the U.S. daily newspapers by then, along with the Thorne and other single type machines. There had been massive disruption in the composing rooms of these papers as hand compositors were replaced by many fewer machine operators.
And the parallel to be noted is that newspapers had consumed the vast majority of hand set type cast by the various foundries. By 1890, the linotype was making serious inroads into that business and then by the time of the 1897 period I am now reading about, commercial printers and book publishers had taken to adopting the line casting machines to supplant hand setting of type. The January 1898 IP noted that “300 dailies of medium size and circulation were using from three to six linotype machines each.” I think that perhaps both the perceived and then real threat of the conversion of hand set type to machines lead the various type foundries to think survival, above and beyond the serious price cutting that was happening prior to the formation of ATF in 1892. The linotype was at the root of that panic that caused the formation of ATF.
The practice of using electrotyped matrices and stealing other foundries’ designs was a common practice. The real meat of type production was in body type used by newspapers and magazines. Foundries were generally located near their major users because of the cost of shipping large tonnages of type. Thus the eastern foundries and those in the “West,” primarily Chicago, St. Louis, and Cincinnati. There was a vast stretch of nothing between those and the true West of California where the remaining foundries were located. But the linotype, followed by the Monotype and later Intertype pretty much limited the remaining type production to specialty, advertising and display type. Where hand set type survived was at the weekly newspaper level—our paper here in Silverton did not get its first linotype until about 1929, and I briefly worked at the Canyon Courier in Evergreen, Colorado in the early 1950s hand setting type for that weekly paper though the bulk of their type was set by linotype in Denver.
Anna,
Pay careful heed to what Fritz has just laid out for you as to the single most important factor that led the the demise of most of the players in the typefounding industry.
Using electrotyped matrices to steal other foundry’s designs was a very common practice that had a miniscule effect on the demise of the foundries.
You may want to rewrite your bold statement to be more historically accurate. Many of us are decades into our own studies and research and have trouble enough keeping the facts straight.
Kudos to Fritz for hitting the nail on the head.
Rick
In some more Inland Printer reading tonight, I read an article about how the electrotype process greatly expanded the ability of foundries to come up with new designs. While steel hand made punches had been the norm, it was found that a type character could be engraved on a piece of soft type metal and then an electrotype could be made to form a matrix for casting. There were not that many people available who could hand engrave steel punches so a better, faster method was developed using the electrotype process. The introduction of the Benton engraving machine later on then lead to a further revolution in making matrices. Monotype used the electrotyping process extensively in the production of flat mats for borders, ornaments and some type faces.
Fritz - I’d be interested in the exact citation for the Inland Printer article you’ve been reading, so I can add it to my list. I’ve been collecting all references I can find from the 19th century (plus some from the early 20th) documenting the importance of (first) hand and (then) machine patrix engraving. (“Patrix” here as a term meaning an original pattern type cut in soft metal from which a matrix will be electroformed; there was no standard term, but Jim Rimmer called them patrices, and that’s good enough for me.) The list (with quotations) so far is at:
http://circuitousroot.com/artifice/letters/press/typemaking/the-issue-of...
In working through this, it has become clear to me - though I am not quite yet at a point where I can prove it beyond doubt, and too much may have been lost ever to reach such a point - that from the middle of the 19th to the middle of the 20th century patrix cutting was not only common, but indeed the dominant method of producing display types. [There were important exceptions, of course - the linecasting manufacturers, English Monotype (but not, as Fritz points out, pre-War Lanston), and I suspect Stempel (through its associations with Mergenthaler.)]
This technology was erased from the history of type-making as it has been taught in America (but not in Germany, for example, where it is documented as just another of the ways to make matrices - see for example various publications of the Bauer foundry, and Bohadti’s _Die Buchdruckletter_). This has led to curious mistakes. For example, in discussing Wedding Text (1901), McGrew (who certainly knew type!) attributes the delay in its introduction to a “new method of cutting [in typemetal],” yet this was simply a method that Benton had been using from the beginning (matrix engraving was the new technology for him; the patent for his patrix and punch engraving pantograph was filed in 1884, but the one for the matrix engraving machine not until 1899). This amnesia has also led to several more-or-less widely known illustrations of patrix engravers being mis-identified as punchcutters in steel. See, for examples, the eight illustrations in the first section of an annotated bibliography of punchcutting literature at:
http://circuitousroot.com/artifice/letters/press/typemaking/literature/p...
The reasons for this historical erasure are complex, and I’m tempted to go on at great length about them here. Don’t worry - I won’t. Briefly, I think that (in general terms) it was a combination of factors: the method was probably always looked upon defensively by typefounders because the same electroforming technology was indeed used to pirate types (and so typefounders didn’t talk about it as much), its use in America must have declined after ATF moved to direct matrix engraving (where in Europe the more diverse foundries there continued to employ it), and perhaps most importantly much of the history of the technology of “how type is made” was written by people in a rather romantic, William Morris inspired, tradition which skipped back over all industrial methods.
Sorry to have hijacked a thread here, but the matter of patrix engraving and the need (in my opinion) to restore it to its rightful place in the history of type-making techniques is something of great interest to me. I suspect it may bore most people, though. I’d be happy to follow up on this, but perhaps offlist might be best.
Regards,
David M.
www.CircuitousRoot.com
I guess I have my homework assignment. The article in the IP about electroforming matrices was in a long article about electrotyping and not about type casting. And that’s where some of these little gems are found. The writers of that era could beat a horse to death before they got to the point, so I typically avoid the pages written about photoengravings and early lithographic techniques. The December 1897 article on Machine Notes and Queries spanned p.318 to p. 322, and was set in what looks like 8 pt. type, and even with a couple of halftones thrown on those pages, that’s still a lot of reading material to wade through.
I cannot quite express how much I envy you (Fritz) your run of Inland Printers. A magnificent resource!
For those of us who have to deal in digital surrogates, vol. 20 of the IP, which runs from Oct. 1897 to Mar. 1898, is online at:
https://books.google.com/books?id=b9dGAQAAMAAJ
(if for some reason Google isn’t serving this internationally, I’d be happy to put a PDF up somewhere)
I couldn’t find a reference to matrix making in the pp. 318-322 Machine Notes & Queries column (it’s probably there, but as you say it’s a lot of material in small print). There are quite a few more references in it to typesetting (vs. composition casting) machines than I expected - another bit of forgotten history.
Perhaps you may also have been thinking of an article later in the same volume, on p. 621 (v. 20, no. 5 (Feb 1898)): the first of Wm. Loy’s series “Designers and Engravers of Type” (which series Steve Saxe has reprinted as the beautiful book “Nineteenth Century American Designers and Engravers of Type”). Loy writes:
“… The discovery of the electrotype process of multiplying matrices became an incentive to type foundries to create new faces, resulting in a bewildering variety of slightly differing styles of type. This made it possible to bring out new styles at a moderate cost, as the pattern letters are cut on soft metal and electrotyped, instead of the old method of cutting everything on steel. …”
Loy goes on in his next paragraph to describe the pantographic cutting of “pattern letters” and the direct pantographic engraving of matrices.
Regards,
David M.
www.CircuitousRoot.com
I guess if one sits on one’s rear long enough, additional effort can be spared. My Vol. 20 is sitting at home, so David’s reading of the IP online beat me to the punch. Unfortunately, what is missing in my bound volume are the covers for this series of magazines which included some by J.C. Leyendecker. His cover for the April 1897 IP was in Vol. 19 which I have and fortunately that book includes the covers, such as this one:
https://www.flickr.com/photos/53177163@N00/11525619005/in/photolist-dBV4...
The Loy article was the introductory one announcing a forthcoming series of stories in future Inland Printers covering the designers of type of that time period.
Google utilized the library collection at Stanford University for some of their first digital work of putting books on line, I guess because Stanford is a few minutes drive from Google’s headquarters. But, remarkable as their effort has been, when I called up David’s link, Google lists “Maclean-Hunter Publishing Corporation, 1898” as the publisher, and of course, for the Vol. 20 it actually was “The Inland Printer Company” that was owned by Henry O. Shepard, who owned the printing company by the same name. Maclean-Hunter didn’t own the IP until mid-twentieth century. M-H is a Canadian publisher that purchased a number of trade publications in the United States. Perhaps whoever did the oversight on producing this for Google went to some university down the street from Stanford, but I at least went to the high school across the street from Stanford though not much scholarly benefit came my way from that association.
Henry O. Shepard is another whole topic but a school was named after him in Chicago and it contained this elaborate leaded glass window celebrating him as a printer:
http://www.publicartinchicago.com/smith-museum-printers-history-by-thoma...
Unfortunately, the Smith Museum where the Shepard widow was displayed at Chicago’s Navy Pier has closed as of October, 2014 (http://www.chicagotribune.com/news/ct-navy-pier-stained-glass-museum-201...). The Smiths, who the museum was named after, established Illinois Tool Works that owned Vandercook and Sons from 1967 until ITW closed Vandercook and sold the parts business to several employees who renamed it Vandersons, which I now own—interesting printing twist to the Shepard window.
An aside to this interesting discussion: Thank you, Fritz, for the pointer to that window — the depiction of the Columbian joins my photo of the bas-relief of one at the offices of the Sydney Morning Herald. Columbians in public art — great!
Bob
But back to the original post about the almost ruination of the type founding industry by Dauchey. In that same Vol. 20 of the IP is a long article about Richard Smith, one of the Smiths in MacKellar, Smiths and Jordan Foundry located in Philadelphia.
Smith really did quite well in the type business and I doubt that his fortune was placed in danger by Dauchey. By the time the story about him was written in 1897, he had set about funding the Smith Memorial Arch in 1891 as well as the Smith Memorial Playground and Playhouse that was completed in 1899 and is still very much in use. Smith had a statue of himself placed in the memorial arch but was surrounded mainly by Civil War generals, a not too subtle way to get himself memorialized as well as getting the arch approved by the city for placement in Fairmount Park. The memorial arch came about from a $500,000 gift Smith made to have it designed and built. Aside from the Children’s Playhouse, which is really a good sized mansion, he also donated a steamboat for the children’s use. These are not the marks of a type foundry owner whose business was forced to join the “Typefounders Trust” to survive economic hard times.
The current take on Smith’s somewhat self-indulgent gift to the City of Philadelphia is reflected in the academic interpretation of his efforts, which probably would make him chuckle if he were to hear them as in this video:
https://www.youtube.com/watch?v=D-lu8ADw01s
And a more recent video taken with a drone of the memorial:
https://www.youtube.com/watch?v=eJeOtsGefr8