Calculating new spring size – Peerless No1
Hi there,
I am currently having issues with the roller springs on my Cropper, Charlton & Co Peerless No.1 (8” x 5”) they appear to be worn out and not have enough tension to pull the rollers back as the roller runners slide up and down the rails instead of roll.
The previous owner had applied wooden blocks in front of the springs and metal braces at the rear to keep them in line.
I was thinking of buying a new set of springs and I was wondering what would be the best way to calculate the right size if the ones on the press currently are worn/need assistance.
I have attached some photos and a rough diagram of sizes, any help would be greatly appreciated!
Thanks,
Kris
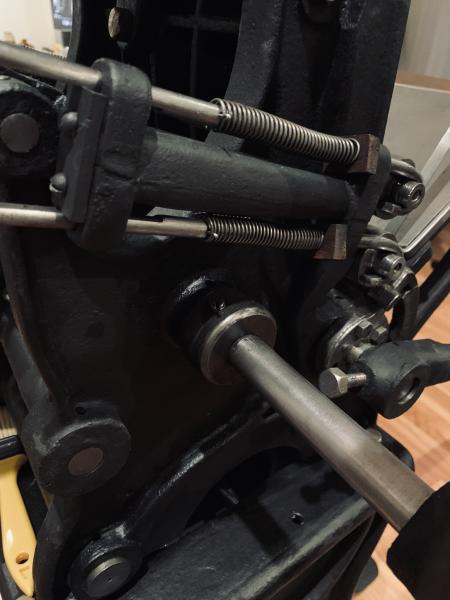
1.jpg
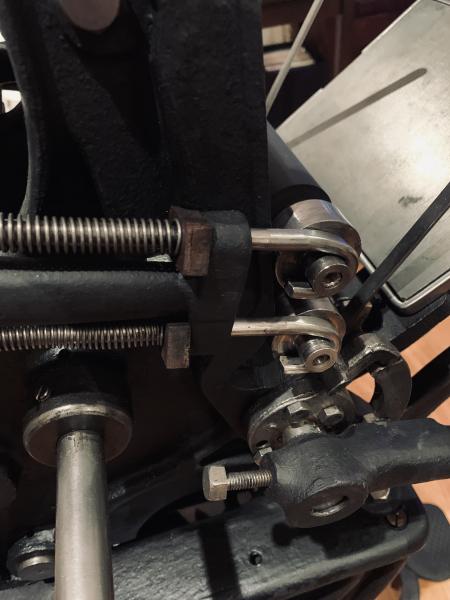
2.jpg
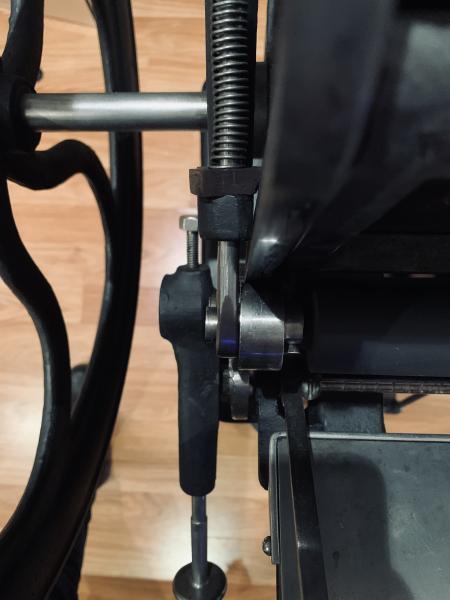
3.jpg
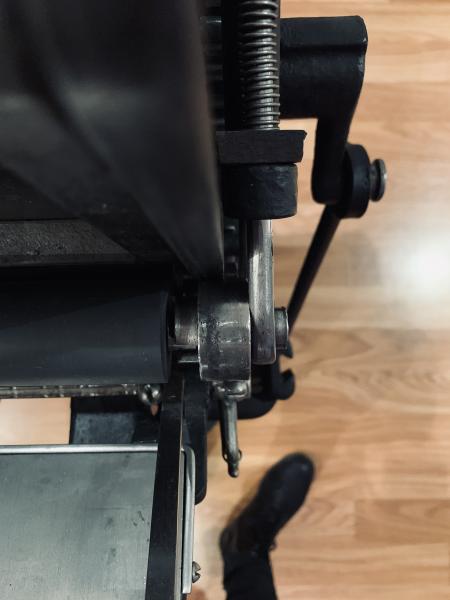
4.jpg
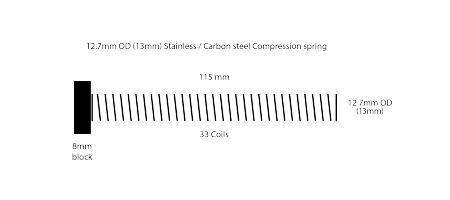
Cropper Springs.png
i imagine the rollers are turning on the shaft real freely
I would first make sure your tracks and roller trucks are totally dry and clean. (But you have probably done that, no?)
After that, just a very small pinch of corn starch on the tracks to pick up any remaining residue.
You’re running metal against metal and that would have a tendency to slip anyway.
Metal on metal shouldn’t slip at all. If the trucks are slipping, either there’s still some contamination on the trucks/rails, a flat spot on the truck, a dip on the rail, or excessive friction at a bearing location (e.g. the hook).
Thank you all for the responses!
The roller trucks are completely dry although I have noticed that some of the hooks grab the roller ends very tightly, almost jammed on. Should I try and loosen the grip on the hook by bending back them a little?
Another thing I noticed and you may be able to see in the last two images is that the roller trucks seem to be overhanging the rails on the right side. (almost half the truck on the rail in comparison to the left.) Is this normal?
Also; should I replace the old springs to eliminate the need for the wooden blocks?
Thanks again for your time,
Kris
If the hooks are grabbing the shafts, then either they need a -little- oil or they’re just too tight- the shaft should rotate freely; if not, you may need open up just a touch. I suspect that’s the real problem, could be those aren’t original-spec hooks.
It does look like the entire roller assembly is a bit off to the right, but it also shouldn’t matter much as long as the trucks are supported and nothing is rubbing or binding.
I would not replace the springs (yet) and I would remove the blocks as I view them as likely being a band-aid for another problem. Start by making sure that everything move freely (except for the trucks on the roller shaft).
z!
Thanks for the notes zbang, the shafts are gripped very tightly by the hooks (limited rotation without force) so I feel like the hooks or the roller trucks may be from another press?
What would be the best way to loosen up the area in the hook? Bending the hook? Filing? I tried oil but they still had limited movement.
I have also been trying to figure out why the roller assembly is offset so much at one side.
As an exercise I stuck my Adana 8x5 rollers and trucks (nylon) on the press and they run up and down with no problem, the roller rubber and trucks are thinner so would not reach anything type high but it’s interesting it had no issues.
I think the trucks may also be why the roller assembly off I have attached an image of the rollers and trucks I have vs the Adana 8x5s both on press.
Thanks so much for taking the time a lot of this is beyond my expertise!
Right Side
Left Side
Peerless vs Adana 8x5
Kind of hard to say what’s the best path without looking closely at the roller shafts and hooks, but things I’d be looking for-
Do the shafts have any burrs (in the bearing region)? Those can be removed by the gentle application of a fine flat file (not sandpaper).
Are the shafts actually round or have they been squashed a little (I think this is not likely) ? You need some good calipers to measure this, but in a pinch, smear the bearing area of the shaft with magic marker, try it in the hook, and see where that rubbed off (the high spot) and where it didn’t. You’re looking for an even rub-off (or none).
(Same for the hooks)
Does the “hole” in the hooks look like it’s be squeezed in one direction or is it round?
If the shafts are out of round, my first stop is a fine flat file and carefully taking off any obvious high spots. A couple of thousandths can make a difference if the hook is tight. Go slowly and recheck often, and be careful not to make a flat spot on the shaft (keep it and and the file moving to avoid that).
If the hooks seem squashed, and that may be hard to tell, look closely at where they’re rubbing. Is this a single or two small spots (<15-20 degrees) or a large radius? A couple of small spits can be worked over with a small half-round file, if it’s a larger area I’d probably start with a round file that’s the same diameter as the shaft or a dowel and 400-grit sandpaper. Again, go slowly and check things often. And be careful to keep the file/dowel perpendicular to the hook.
I probably wouldn’t try to unbend the hook unless it was “extra closed” and I had a good vice and tools. Since the shaft does fit and rotate somewhat, this shouldn’t be necessary.
As with all press mechanics- go slowly and be patient :) It’s easier to remove a little at a time than to put it back.