Trouble with Poco Cotter Pin
Hello all,
I recently had my poco welded and the man that welded it removed the lever… and while trying to get it back on, it became pretty stuck. I know that the pin is only barely engaging the shaft, but it won’t budge… in or out.
I would like to get it out, because I’m not even sure it’s in the right orientation… does anyone out there have suggestions?
Any help would be greatly appreciated… I would love to actually start using my press!
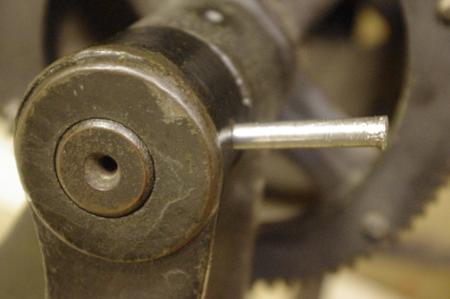
pin1.jpg
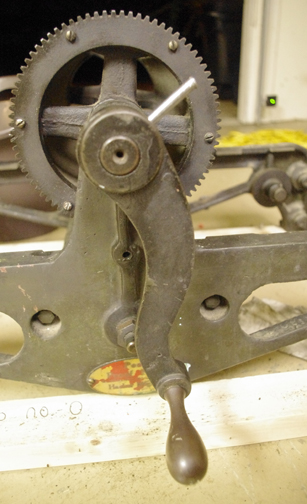
pin2.jpg
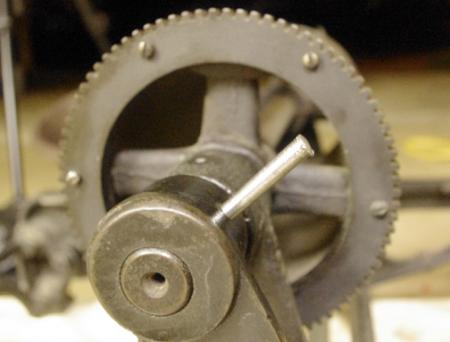
pin3.jpg
Drive it out from the other direction.
That is, get a skinny piece of steel (perhaps even a nail), long enough to reach all the way through the base of the handle and thin enough to reach into the hole used by the cotter pin. Put it in the hole and tap it gently with a hammer.
That should get it out.
Then, before you try again, experiment with the various pieces to see how it goes back together. First play with the pin and the handle to see which way it should fit (there’re 2 possibilities). Then try to see which way the pin fits through the axle (again, there’re 2 possibilities).
Finally, put the handle on the axle and put the pin in place.
Preston
a nail won’t work. way too soft. you need the proper size “pin punch”. look from the other end of the hole and see if the holes look lined up properly.
next, you will HAVE to determine if the pin and hole is tapered. is the lever in the correct orientation to the gear? once the pin is out you will need to see if the pin (you may need a new one by the time it is out) fits better from one way or the other. a skilled machinist/mechanic would be a big help here
Enter a machinist with a Poco. Although Ericm points out the correct tool, most people do not have a machinist punch narrow and long enough to do this. I don’t think it is necessary here. A tapered pin(which it is) put in backwards should not be that difficult to dislodge. Try what Preston suggests but file or cut off the point of a 16d nail if you can. Both the hole and the pin are tapered. Your pin is put in the wrong side which is why it did not go in all the way and is now stuck. If gentle tapping does not do it, I would give it a sharp hit. It needs to come out and be put in from the correct side with the handle in the correct orientation as Preston points out. (Tapered pins are a hardware store item.)
A good choice for a pin punch is a concrete nail — they are hardened and tempered like a pin punch would be but not as nicely machined. Finding one small enough might be challenging, but a good hardware store should have them. Do grind the end flat, otherwise the point could dimple the end of the pin, spreading it and making it harder to move.
Bob
Thanks guys! I assumed it was tapered, but I also assumed that the welder put the pin on the correct side (it was tapped into the handle when I got it)… but now I am sure my second assumption was incorrect. I will try the filed down concrete nail and see if that works. (Let’s hope it works!)
Use a grinder on the nail — it’s hardened and will destroy a file if it’s correctly done. There are two kinds, square or rectangular (cross-section) cut nails with blunt ends and round nails with pointed ends. Either one should work. Once you get the pin out you should probably try to get an new one rather than re-use the damaged one.
Bob
Bob- I am definitely going to try and find a new pin.
milkandtoast,Ace hardware sells tapered pins.
a good life lesson never assume anything.
best james
Would it be a really bad idea to try and cool the pin down? I know cooling metal makes it more brittle, and cast iron is pretty much the most brittle you can get, but I wondered if I covered all the cast iron and just sprayed coolant on the pin if that might help to loosen it up?
I’ve never heard of cooling, i think it would make the metal brittle, i had to remove pins from my windmill and we heated them. also you can drill the pins out. Dick G.
I’ve never heard of cooling, i think it would make the metal brittle, i had to remove pins from my windmill and we heated them. also you can drill the pins out. Dick G.
I guess you could cool the steel pin without problem (I assume you aren’t going to get it all that cold). But seems like overkill. Just give it a tap as outlined above.
Sart simple; if that doesn’t work, try other tricks.
Preston
I’ve tried tapping it out, and it’s not budging… hence the tricks
can you see from the other side if the holes are lined up properly? if they are not, it is possible you are not even tapping against the pin, but instead the center shaft. you may have to drill this out to relieve pressure. it also possible that the end of the pin is now mushroomed a bit and will not go out the smaller end. i tried to illustrate this.
pin in hole.JPG
Ah, I see. Well, spray it with freon (or whatever) by all means. If the pin gets brittle and breaks, ok. At least it’s out.
Drilling is another destructive approach. I’d start with your cooling idea.
Good luck,
Preston
preston- I’m not concerned as much with the pin getting brittle, but the iron. It would really suck to break the handle!
you will get more out of the freon than the part of the pin that is stuck.
cooling will not do what you think on such a small piece. it really works best on something hollow.
cut the pin off just above the entry point. center punch and drill it out. starting with a small drill size then work bigger.
Jeez,,, i’m ready to come wherever and do it myself….
Try soaking with penetrating oil, like liquid wrench, let it soak for a while then try driving it out. Dick G.
thanks eric- the cooling method was my step-dad’s idea… it scared me, so I figured I would bring it to briar and see how you guys reacted. I think you are right about the “mushrooming” the pin can’t be engaged by much, so to me, it makes the most sense that the point on the inside has flattened out some. Drilling seems to be the next best thing, so I’m going to give that a try.
dick- I soaked each side with penetrating oil over night (over two nights) and it still didn’t budge.
Have you tried grabbing the pin with Vise-grips and twisting it out, or tapping the Vise-grips with a hammer? The pin should be sacrificed at this point in order to preserve the tapered hole.
just be careful and go slow.
is this the same pin you sent out with the unit? if not, it could easily be a size too large. that would stick it in there real good. if your welder took the pin out,it is somewhat common that these are not reusable. he may have used the wrong size.
Thanks everyone for the imput. I found a friend of a friend who’s a mechanic with the right punches, and the pin came out, no problem! Yay!